Rubber hydraulic hoses
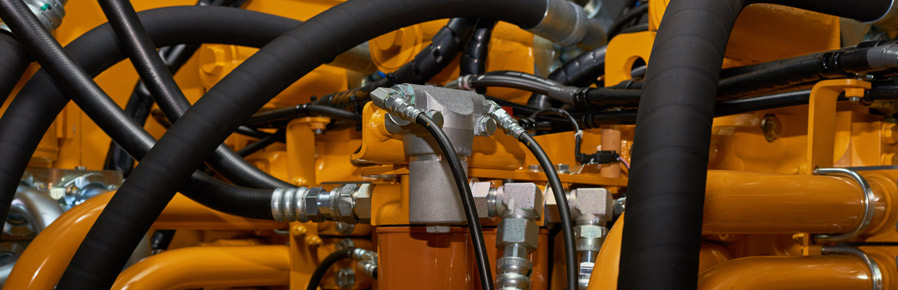

Rubber hydraulic hoses – general information
Rubber hydraulic hoses are used in high pressure hydraulic systems for control and power supply. They are designed to transfer hydraulic oil primarily (hydraulic fluid compliant with ISO 6743-4, apart from HFD R, HFD S and HFD T fire-resistant fluids). For other applications (e.g. for compressed gases) always contact Technical Department of TUBES INTERNATIONAL®. For water, water-based fluids and air, the maximum working temperature is +70°C. For air over 17 bar, the external layer of the hose should be pinpricked and have additional protection.
Construction and features of rubber hydraulic hoses
Typical hydraulic rubber hoses can be classified into three different construction types:
Hoses with textile braid
(one or two) Hoses with compacted
steel wire braids
(one, two or three) Hoses with steel wire spirals
(four or six)
Hydraulic rubber hoses are manufactured in imperial size with standardized inside diameter. The most popular standards setting the requirements for hoses are: European standards – EN, international ISO and American SAE. The symbol of the standard and the most important data (diameter, working pressure and production date) are marked on the hose. Additionally, there may be a specific name on the hose that is given by a producer or customer.
Hydraulic hoses that exceed given standards
Greater flexibility
Hydraulic hoses whose minimum bend radius is smaller than standard.
Higher pressure parameters
Hydraulic hoses whose maximum working pressure is higher than the requirements given in the standards. This extends the scope of hose applications while keeping the safety factor and the same hose diameter, so there is no need to change it (e.g. to a smaller one) or change its type (e.g. from a double braided to a spiral hose).
Higher temperature parameters
Hydraulic hoses have a specific temperature range in which they should operate. This range is from -40°C to +100°C (with peaks up to 125°C) for hoses with textile braids ( 2TE, 3TE type), with compact steel wire braids (1SC, 2SC,1SN, 2SN), and for a certain group of hoses with spiral braids (4SP, 4SH). For spiral hydraulic hoses with constant working pressure regardless of diameter (R12, R13, R15) the range is from -40°C to +121°C (with peaks up to 125°C). Sometimes the operating temperature of a hydraulic system may happen to be higher than the temperature of standard hydraulic hoses. If the recommended temperature is exceeded, the rubber starts to lose its flexibility and stiffens, then leakage starts to occur at hose ends, close to the fittings. In such cases, hoses with a higher operating temperature range should be used.
Greater abrasion resistance
The outer layer of rubber hydraulic hoses manufactured according to popular standards has limited abrasion resistance. Abrasion resistance tests are performed according to EN ISO 6945 standard. It defines the weight loss of a hose sample after a specific number of cycles and vertically applied force (e.g. an average weight loss is 0.5 g for type 1SN and 2SN hoses tested to 2 000 cycles at vertical force (25±0.5 N).
To increase the abrasion resistance of the outer layer, manufacturers apply an additional layer (e.g. UHMWPE Ultra-high molecular weight PE – cross-linked polyethylene). Then, there is no need to apply an extra protection cover (e.g. hose protection spiral).
Longer service life
The service life of hydraulic hose assemblies under actual operating conditions depends on many factors, including:
- fatigue strength of a flexible hose assembly exposed to variable internal pressure, bending, internal and external temperature changes,
- ageing resistance (natural loss of mechanical properties of hose material),
resistance to external damage.
The fatigue strength of the hose assembly can be tested by conducting hydraulic-pressure impulse tests with or without simultaneous flexing. Test procedures are described in the standards (ISO 6803, ISO 6802, ISO8032). These standards determine the required resistance to pulsating pressure for particular hose types. The required resistance means the number of pressure pulsation cycles (impulses) the hose must withstand. The frequency of pulsating pressure is quite high (about 1Hz), the test pressure is from 100% to 133% of maximum working pressure, and the test temperature is elevated (100°C). Test results do not give the precise service life of the hose assembly under actual operating conditions. However, they help to check whether a hose meets or exceeds the requirements of the standard and compare hoses from different manufacturers against each other.
The service life of hydraulic hoses is affected by many external as well as internal factors. Assuming that a particular hose has been properly selected in terms of operating parameters (pressure, temperature, medium, etc.), the question arises of how long the hose will last. At this stage of hose selection, we can only rely on the additional information provided by the hose manufacturer. And in this case, such information could be data on strength tests (e.g. for pulsating pressure). The resistance to pulsating pressure is defined as the number of pressure impulse cycles the hose should withstand when tested according to the procedure specified in ISO 6803.
EN853 standard for type 2SN hoses specifies a minimum of 200 000 impulse cycles that the hose must withstand at a pulsation pressure of 133% of the maximum working pressure.
EN857 standard for type 4SH hoses specifies a minimum of 400 000 impulse cycles that the hose must withstand at a pulsation pressure of 133% of the maximum working pressure.
List of products:
Hydraulic hoses, with textile braid (2TE, 3TE)
Hydraulic hoses, with steel braid (1SN, 2SN)
Hydraulic hoses, with steel wire spiral (4SP, 4SH, R13, R15)
Compact hydraulic hoses, with steel braid (1SC, 2SC)
Hydraulic hoses, with enhanced flexibility
Hydraulic hoses, with higher working pressure
Hydraulic hoses, for higher temperatures
Hydraulic hoses, with longer service life
Flame resistant hydraulic hoses
Hydraulic hoses, mining compliance
Hydraulic hoses, railway compliance